Best Practices for Implementing Yard Management Systems in Lumber Storage Facilities
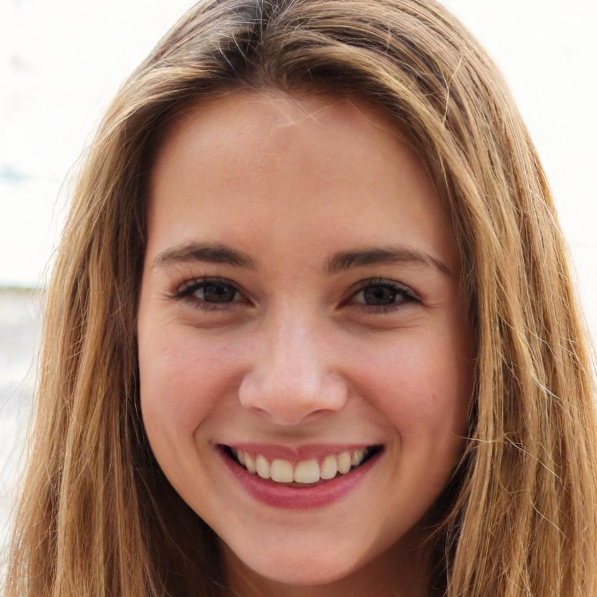
AUTHOR: Katie Conway
Katie Conway is a passionate author and logistics enthusiast specializing in warehouse organization, pallet racking safety, and efficient storage solutions. Join Katie on a journey of discovery and growth as we explore the ever-evolving world of logistics and supply chain through her blog.
Yard Management Systems (YMS) play a crucial role in optimizing operations and enhancing efficiency in lumber storage facilities. These systems enable effective inventory management, streamline workflows, and improve overall productivity. Implementing a YMS requires careful planning, customization, and employee training. Racks for lumber often have structured and vertical storage solutions. They provide secure support, preventing warping or damage to the lumber while maximizing the use of available space. The combination of YMS and racks is essential for effective lumber storage, enabling facilities to optimize their processes, increase productivity, and deliver superior customer service.
By following these guidelines, facility managers can ensure a seamless integration of the YMS, maximize its benefits, and achieve operational excellence.
Let’s explore the best practices below:
Define Clear Objectives
Before implementing a YMS, it is essential to define clear objectives that align with the facility’s goals and operational challenges. Identify the pain points and inefficiencies within the current yard management processes. Is there a need to reduce truck turnaround time, enhance order accuracy, minimize product damage, or improve inventory management? By understanding the specific challenges, facility managers can set realistic and measurable objectives.
Clear objectives provide a roadmap for YMS implementation and help measure the success of the system. These objectives should be communicated to the entire team to align everyone’s efforts toward a common goal. For instance, reducing truck turnaround time may involve implementing automated check-in/check-out processes, optimizing yard layout, and improving communication channels.
Conduct a Thorough Site Analysis
Before implementing a YMS, it is crucial to conduct a thorough site analysis of the lumber storage facility. Evaluate the layout, workflow, and operational requirements of the yard. Consider factors such as storage capacity, traffic flow, safety regulations, and environmental constraints. During the site analysis, identify existing bottlenecks, areas for improvement, and potential integration points for the YMS. Evaluate the current technology infrastructure and determine how the YMS will integrate with existing systems, such as warehouse management systems (WMS) or transportation management systems (TMS).
A comprehensive site analysis helps customize the YMS to meet the unique needs of the facility. For example, if the facility frequently deals with perishable lumber, temperature monitoring and alerts can be integrated into the YMS to ensure the quality of the inventory.
Get best practices for reducing dwell time
Invest in Reliable Technology
Choosing the right YMS technology is critical for the success of implementation. Consider a YMS that aligns with the facility’s specific requirements and integrates well with existing systems. Look for features such as dynamic appointment scheduling, digital check-in, real-time visibility, automated data capture, analytics and reporting.
Reliable technology ensures accurate tracking of inventory, efficient yard operations, and data-driven decision-making. When evaluating YMS vendors, consider factors such as their industry experience, customer reviews, and track record of successful implementations. Engage in discussions with vendors to understand their support services, scalability, and customization options.
Pilot testing the YMS in a controlled environment can help validate its effectiveness before full implementation. This ensures that any issues or glitches are identified and resolved before rolling out the system facility-wide.
Train and Educate Staff
Proper training and education are vital for the successful implementation of a YMS. Provide comprehensive training to employees, including yard operators, supervisors, and administrators, on how to effectively use the system. Educate them about the benefits of the YMS and how it will improve their daily workflows. By understanding the YMS’s capabilities, such as real-time tracking, streamlined communication, and efficient task assignment, your team gains valuable insights into optimizing yard operations. Improved visibility and coordination mean reduced wait times, faster truck turnarounds, and minimized delays, leading to a smoother, more organized workflow. Empowering your staff with YMS knowledge fosters a collaborative environment, where everyone can actively contribute to maximizing efficiency and ensuring a seamless yard management process. Familiarize employees with the YMS advantages, like understanding how it simplifies tasks, how it reduces manual errors, and how it enhances the overall productivity. With its potential to minimize waiting times, expediting truck movements, and ensuring smoother logistics coordination, your workforce will embrace the YMS as a valuable tool to improve operational efficiency.
The training should cover various aspects, including system navigation, data entry, reporting, and troubleshooting common issues. Emphasize the importance of accurate data input and the impact it has on the overall efficiency of the system. Conduct regular training sessions to keep employees updated on system upgrades or new features.
Additionally, create a support system for employees to address any challenges they may encounter while using the YMS. Establish clear communication channels to encourage feedback and suggestions for system improvements. This fosters a culture of continuous learning and improvement within the facility.
Streamline Communication
Effective communication is vital for smooth yard operations. Implement a centralized communication system within the YMS to facilitate real-time communication between yard operators, truck drivers, and other stakeholders. Automated alerts, notifications, and electronic documentation can help minimize errors, delays, and miscommunication.
By streamlining communication, the YMS reduces the reliance on manual communication methods like phone calls or paper-based documentation. This, in turn, minimizes errors, improves efficiency, and enhances overall operational visibility.
Schedule a FREE yard audit with Vector
Optimize Yard Layout and Traffic Flow
Efficient yard layout and traffic flow are essential for maximizing storage capacity and minimizing material handling time. Designate specific areas within the yard for different types of lumber and clearly label them. Implement traffic management strategies to reduce congestion and enable smooth movement of trucks and equipment.
Utilize the YMS to track yard occupancy, allocate parking spots, and optimize load sequencing. This allows for efficient utilization of space and minimizes the time spent searching for inventory. Automated workflows within the YMS can help prioritize tasks, assign resources, and optimize routing for increased efficiency.
Regularly evaluate the yard layout and traffic flow to identify opportunities for improvement. Analyze the data collected through the YMS to understand patterns and make data-driven decisions. Consider incorporating technologies like RFID or barcode scanning to enable accurate and real-time tracking of inventory movements.
Utilize Data Analytics
Leverage the power of data analytics provided by the YMS to gain valuable insights into yard operations. Analyze historical data to identify trends, bottlenecks, and areas for improvement. Utilize data visualization tools to present the information in a clear and actionable manner.
The YMS can generate reports and analytics on various aspects such as inventory accuracy, truck utilization, or yard congestion. These insights can help optimize workflows, make data-driven decisions, and implement continuous process improvements.
By utilizing data analytics, facility managers can identify patterns of inefficiency, predict demand fluctuations, and proactively address operational challenges. Regularly review key performance indicators (KPIs) such as truck turnaround time, order fulfillment accuracy, and inventory accuracy to monitor the impact of the YMS implementation.
Monitor and Evaluate Performance
Continuously monitor the performance of the YMS and evaluate its impact on yard operations. Track KPIs and compare them against the defined objectives. Identify any shortcomings and address them promptly to ensure ongoing optimization.
Regularly engage with stakeholders, including employees, customers, and vendors, to gather feedback on the YMS’s performance. Conduct periodic reviews and audits to identify areas for improvement and implement necessary changes.
Embrace a culture of continuous improvement by fostering collaboration between different departments and encouraging employees to suggest process enhancements. Regularly communicate updates and share success stories to build momentum and ensure that the YMS remains a priority within the organization.
Implementing a Yard Management System in lumber storage facilities requires careful planning, customization, and employee training. By following the best practices outlined in this article, facility managers can optimize yard operations, reduce costs, and improve overall productivity. A well-implemented YMS empowers facilities to efficiently manage their inventory, streamline workflows, and deliver exceptional customer service. With clear objectives, reliable technology, and ongoing monitoring and evaluation, the YMS becomes a catalyst for operational excellence and growth in the lumber storage industry.